1885年,一位德国公司的经理不远万里踏上了中国这方土地,他带着说服中国人相信巴斯夫(BASF)染料优点的使命,牵起巴斯夫与中国的缘分。
那年是巴斯夫成立的第20年个年头,时光飞逝。今天,大中华区已经成为巴斯夫在全球最重要的市场之一,同时也发展成为亚太区的创新枢纽。巴斯夫亚太区总裁、大中华区总裁兼董事长柯迪文博士(Dr.StephanKothrade)表示,巴斯夫在中国投资总额已经达到60亿欧元,未来将持续看好中国市场。
研发重点落在上海
顺着时间的脉络,巴斯夫在华业务一直处于不断扩展与深化阶段。1982年,巴斯夫决定直接管理公司在华业务,因此在香港成立子公司—巴斯夫中国有限公司。1986年,巴斯夫在中国建立第一个合资企业:上海高桥巴斯夫分散体有限公司,生产用于涂布纸张和地毯行业的苯乙烯-丁二烯胶乳。之后又相继有数家巴斯夫合资和独资企业投入运营。
2000年,巴斯夫与中国石油化工股份有限公司(下称“中国石化”)共同在南京成立了一家合资企业扬子石化-巴斯夫有限责任公司(下称“扬巴”)。2004年,巴斯夫开始集中管理中国业务,并将大中华区总部迁至上海。
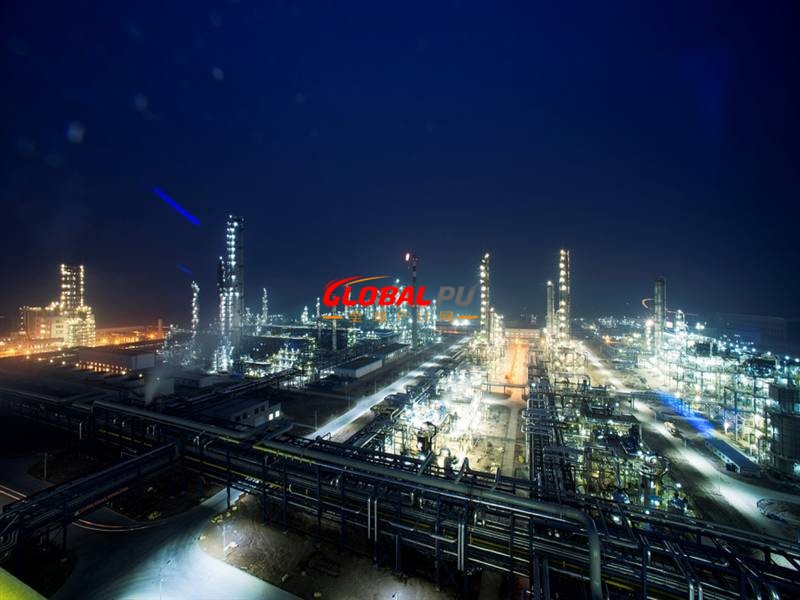
伴随着业务的不断深入,巴斯夫在中国的营业额也在稳健增长。尽管2016年市场环境动荡不安、充满挑战,巴斯夫大中华区作为巴斯夫集团的第三大市场,销售额仍然达到59亿欧元。柯迪文博士向记者表示:“我们持续投资集中在上海和南京生产基地的本土生产能力,以满足下游客户行业的需求。”
毫无疑问,一百多年前,中国对于巴斯夫来说尚是未知的新市场;现在,中国已经成长为巴斯夫不可或缺的一部分。事实上,巴斯夫早已成为中国化工领域最大的外商投资企业。
对于中国市场,柯迪文博士有着自己清晰的战略,其中生产、研发、产品组合管理和市场分销将会成为巴斯夫在华立足的重要抓手。经过几十年时间的迅速增长,中国市场体量已经十分庞大,考虑到中国幅员辽阔,巴斯夫对中国市场进行了全面的业务布局。
“我们已经将生产网络拓展到中国西部地区至新疆库尔勒,并逐步提升重庆二苯基甲烷二异氰酸酯(MDI)生产基地以及与中国石化共同建设的广东茂名异壬醇(INA)生产基地的产能利用率。同时,我们正在通过海内外的资产收购来增强本地网络和产品组合,实现增长。”柯迪文博士表示。
任何一家跨国企业对某一关键性市场进行布局都不是一蹴而就的想当然行为。作为全球化工行业的领军企业,巴斯夫在华拓展秉持着怎样的战略呢?就此,柯迪文博士表示,巴斯夫首先考虑的是在当地有没有重要的行业支撑。另外考虑到化工原料运输的成本问题,也要考虑原材料的可得性。第三就是巴斯夫在当地是否有生产基地,可以与巴斯夫现有的生产资产间产生协同效应。
因此,柯迪文博士进一步向记者表示,“巴斯夫研发的重点依旧会落在上海,生产布局的具体情况可能会更复杂一些。目前巴斯夫主要的生产能力布局在上海以及上海周边地区,还有南京、重庆。”
就在最近,不断看好中国市场的巴斯夫宣布了一系列在中国的新一轮投资。目前,一座总投资额达到1.4亿欧元的新的世界级汽车涂料生产装置在位于漕泾的上海化学工业区竣工投产。而其世界级化工催化剂生产装置也已经在上海正式落成,记者从巴斯夫方面获悉,这也是巴斯夫在亚太区的首套化工催化剂生产装置。
垂直一体化战略
研究巴斯夫的企业管理之道很难忽略其一以贯之的“垂直一体化战略”。最开始,巴斯夫只是一家生产煤焦油的公司。其创始人之一弗雷德里奇有一项见解:如想在化工业务上获得长期成功,必须掌握高质量的生产原料和前体(化工原料生成的前体,再进一步由前体合成产品),由自身积累推动和资助化学研究工作。百年来,巴斯夫引以为傲的“verbund”(德语,意为“一体化”)概念在中国展开。
柯迪文博士向记者表示,“一体化概念核心是,一个反应装置中的产品、副产品甚至废弃物,成为下一个反应装置的原料与能源。”
当分包和众包成为全球企业公认的成本管理之道时,巴斯夫却一直都在实践一体化的理念:90%的原料由自己供应生产;从最基础的化工原料到高端的化工产品,巴斯夫吃足产业链的长尾;甚至各跨国公司下放到各地的采购权,巴斯夫也在通过全球采购一体化小组来收回。
经过百余年发展,巴斯夫的一体化图景越来越清晰:研究和生产在同一地点,生产装置、能源、物流和基础设施合理相连;生产由一个共同源头出发,一家工厂的产品或副产品可能成为下一家工厂的原料。通过这种环环相扣的生产方式,在这个纵向一体化的生产链内实现低能耗高产能,形成规模效益并且创造附加价值。一体化也为巴斯夫更为灵活地应对经济波动、行业周期性和变化的市场需求提供了保障。
一体化体系是巴斯夫最大的优势之一。在一体化生产基地内,各生产装置通过管道网络实现智能化连接。这不仅使化学品运输物流成本大幅降低,还可以节约原材料和能源,充分发挥协同效应。“一体化可以实现能源联动效应,减少能源浪费。”柯迪文博士表示。
以扬巴基地为例,柯迪文向记者介绍到,作为巴斯夫与中石化共同经营的一体化基地,扬巴基地里面一共有多套装置,这些装置用于生产所需的动力,有1/3来自生产基地内其他装置生产过程当中产生的余热。由此导致总体的能耗减少了33%。另外在扬巴一体化基地里,基本实现了基于天然气的热电联产。通过热电联产,除了能源利用效率大幅提升之外,还减少可二氧化碳的排放。“通过热电联产和能源使用一体化,巴斯夫全球能够减少二氧化碳排放达到660万吨。”
传统行业的创新之路
作为传统化工行业企业,巴斯夫在2011年发布“创造化学新作用”的口号时,就曾经表示当代化工行业的创新已经很少依赖于新化学品的开发。
巴斯夫希望通过各学科知识的结合,打造新材料与系统解决方案。
柯迪文博士向记者表示,“巴斯夫保持成功的重要因素就是要不断创新。在下游市场,巴斯夫已逐渐摆脱传统化学品生产商的形象,用其经验和创新与客户合作,嵌入其研发生产进程。例如:巴斯夫与ofo合作,推出了一款采用巴斯夫Elastopan?聚氨酯(PU)制造的双层车胎系统单车“小黄蜂”。
巴斯夫很早就注意到中国轻型车市场的蓬勃发展并通过创新在这一领域进行布局。巴斯夫为吉利汽车推出了排放催化剂,通过较少使用贵金属减少了对环境的污染情况。
由一家化工企业直接渗透入下游产品的设计过程十分少见,但这一工作对巴斯夫而言显得十分轻松:不论是制造复杂的汽车还是看似简单的单车,这些产品所需的功能性材料与化学品几乎均可由巴斯夫提供。
此外,在白色生物技术这一技术领域,巴斯夫正在研究用于化学和生化产品的高效、资源节约型方法和工艺。相对于化学工艺,发酵和生物催化技术正逐渐成为极具竞争力的替代选择。
正因不断的创新和与下游相结合,虽然终端消费者并非会十分熟悉巴斯夫,但其几乎无处不在。